Reduce Downtime by Selecting the Right Screening Media
Choosing the right screening media plays an integral role in reducing downtime and maintaining productivity. Because of this, it is important to look into the benefits and drawbacks of each material before making your decision. Below, we break out the different types of screening media available and what each is good for.
Woven Wire
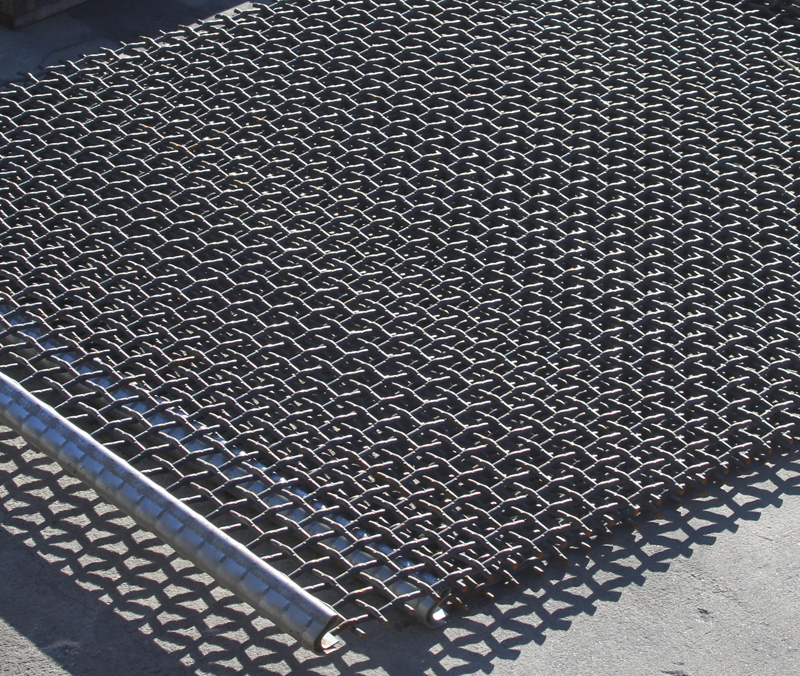
Wire Screens
Wire screens are considered to be the “standard” or “baseline” screening media. These screens come in several different wire types. The two main wire screen types are high-carbon and heat treated. There are different variations of both types depending on what supplier you are working with.
The industry standard, high-carbon or “HC” steel is typically the more cost-effective, lower-end option. Since almost every screen media supplier offers HC steel, it should be available virtually anywhere.
Heat-treated steel is more durable (and more expensive) than high-carbon steel. Screens made with this steel tend to last longer because they can wear thinner before they break and/or fail.
Some manufacturers boast things like “oil tempered,” “gator wire,” or “optimum wire.” These options are all high-carbon steel quenched in some kind of liquid to keep the wire from becoming too brittle in the manufacturing process. The goal is to produce the hardest steel that is still ductile enough to be woven and survive the violent shaking of a screen box.
Wire screens are at a lower cost and offer higher open area than rubber or polyurethane screens, but the wire doesn’t last as long. Having a higher open area means better throughput on your screen decks, higher production and increased tons per hour. However, if the wire screens wear out faster, that can lead to more downtime to change out screens; all of this is not to mention more frequent screen failures can cause contamination of finished products.
As far as wire types, there is stainless steel for corrosion resistance, which can help with throughput and life, but it costs more and is usually softer steel than other options. Stainless steel is mostly used in recycling yards and wet screening. The rest are high-carbon steels with various designations.
Non-Woven Wire
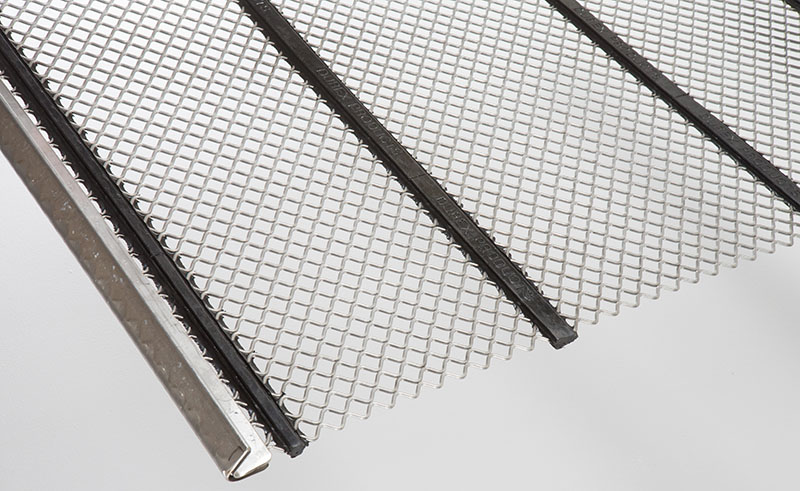
Non-Woven Wire Screen
Stepping away from standard woven wire screens, you then open the door to options like “clean screens.” These are non-woven screens, where the wires run parallel and do not intersect or overlap. The wire is held together with either urethane or rubber. Again, there are lots of variations of this type of screen based on the supplier, but they mostly do the same job of keeping the screen deck from clogging up. However, performance can vary based on the supplier and quality of materials.
Almost all of these types of screens are made with heat-treated wire as high-carbon wire is not able to perform within this type of non-woven screen. There are several different patterns of non-woven screens available, and suppliers tend to offer the same patterns with different names. These types of screens do very well in finishing screens that see smaller material flow across their decks. They do not do well in high-impact and large-material-size applications. Typically, you will never see these on a top deck of a multi-deck screen unit. Instead, they would be on the second or third deck.
Rubber Punch Plate
An option for high-impact and heavy-use jobs is rubber punch plate, which is also available in modular systems as well as tension mats (hooked screen panels). A couple of examples are shown below. Rubber does a great job in high-impact areas as it can take the load and has a very good wear life. The downfall with rubber plates is that they are very heavy and tend to use up a lot of open area. Because of this, the screen produces less material per hour.

Rubber Screens
Urethane Punch Plate
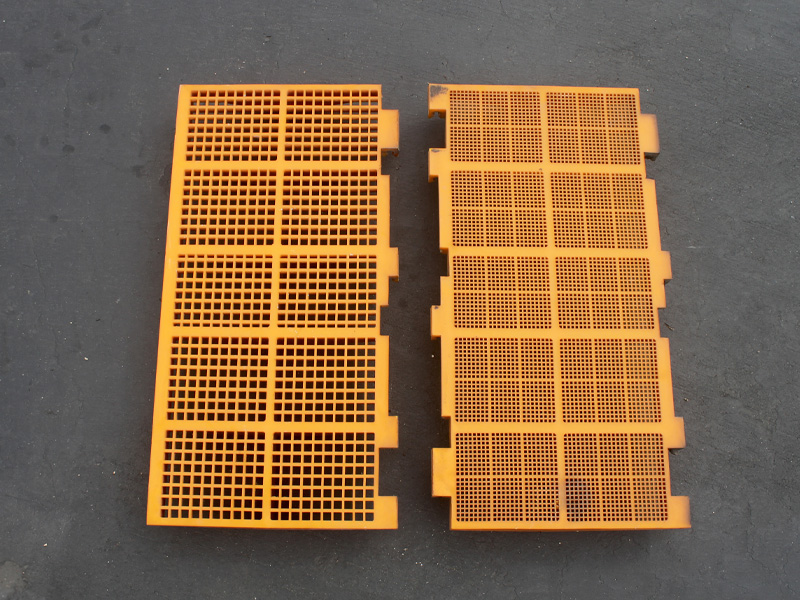
Urethane Screens
Urethane is another media choice. Urethane can handle some decent impact and material flow (though not as good as rubber). Urethane is ideal for wet or “sticky” applications since material does not stick to it. It also has exceptional wear life over most other options.
Both rubber and urethane are available in a variety of hardnesses which are referred to as durometer.
Urethane (like rubber) is available in punch plates, modular panel systems and tension mats. A couple of examples are shown below. Again, a downfall to urethane is a loss of open area which decreases the throughput of the machine. On the other hand, urethane increases wear life and decreases the amount of material that gets stuck in the screen unit. Both rubber and urethane are expensive options, meaning that they are both very application specific.
Many large-scale producers will opt to use rubber and polyurethane screens and counteract the lower open area by having larger screen decks with more screen panels on each deck. This gives you a long life with predictable downtime and keeps up high production numbers. Unfortunately, you have to buy bigger, more expensive screen boxes upfront, and also more expensive screen panels per square foot.
Steel Punch Plate
Another type of media you will find is the heavy-duty screening options like steel punch plate, made from abrasion resistant plate. These options are used in high-impact heavy-load applications. Normally, you will see these on the top deck of multi-deck screen units to get rid of all the large oversized material that is not wanted.

Punch Plate Screens
Many different situations may require one screen versus another, and the best choice of media heavily depends on the application. By choosing the correct screening material you help to decrease downtime and increase your production. Cutting Edge Supply has the ability and the know-how to both help you find the right media and custom make it for you.